4 Problems You Can Avoid With Freight Invoice Management
Freight Invoice Management
It feels great when a freight invoice is correct, but mistakes can occur that will cost you if you don’t pay attention to those invoices. This is why freight invoice management is both common and critical in the shipping industry. A lot can happen between the time you ship an item and when it arrives at its destination, so use your invoice as a final assurance that the journey went smoothly.
This might sound like a laborious extra step, but adding it to your workflow is relatively easy, especially if you want to avoid paying problematic charges. The more you know about invoice management, the more you’ll learn about freight costs that affect every shipment. Learn more about how you can sharpen your shipping skills with this list of problems you can avoid with freight invoice management.
Additional Accessorial Charges
One of the most common charges businesses dispute is accessorial charges, but you won’t know they’re on your bill if you don’t look. An accessorial charge occurs when your freight carrier must perform additional tasks outside their standard services.
On the surface, that may not sound like an issue because if you know you have to pay more for specialized services, then you can make that decision yourself. After all, shipments come in many forms, and the team carrying that shipment can change their practices to accommodate in various ways, depending on the available resources. But that’s the issue—sometimes, an accessorial charge may appear that you didn’t establish with your freight carrier.
At Translogistics, our freight invoice auditing helps by disputing accessorial charges not included in the original quote by the carrier. Common accessorial charges businesses dispute include reweighing, reclassification, detention, and pick-up/delivery attempts. Keep an eye on your freight invoices to always identify charges worth disputing or have peace of mind after reading a clean, correct invoice.
Freight Invoice Management
Common Freight Invoice Disputes
Improperly Classifying Freight
Each commodity routed via the LTL network receives a specific classification before it reaches its destination. It is important that the
Bill of Lading has the appropriate
NMFC & Freight class labeled properly.
LTL freight can fall under 18 different classifications, including:
- Class 50
- Class 55
- Class 60
- Class 65
- Class 70
- Class 77.5
- Class 85
- Class 92.5
- Class 100
- Class 110
- Class 125
- Class 150
- Class 175
- Class 200
- Class 250
- Class 300
- Class 400
- Class 500
The purpose of giving freight a class is to ensure that each shipment is appropriately priced. So, how do you determine which freight receives a given classification? The final classification comes down to details, including shipment density, handling necessities, liability, and storability. Now, let’s explain how those factors play into the classification process.
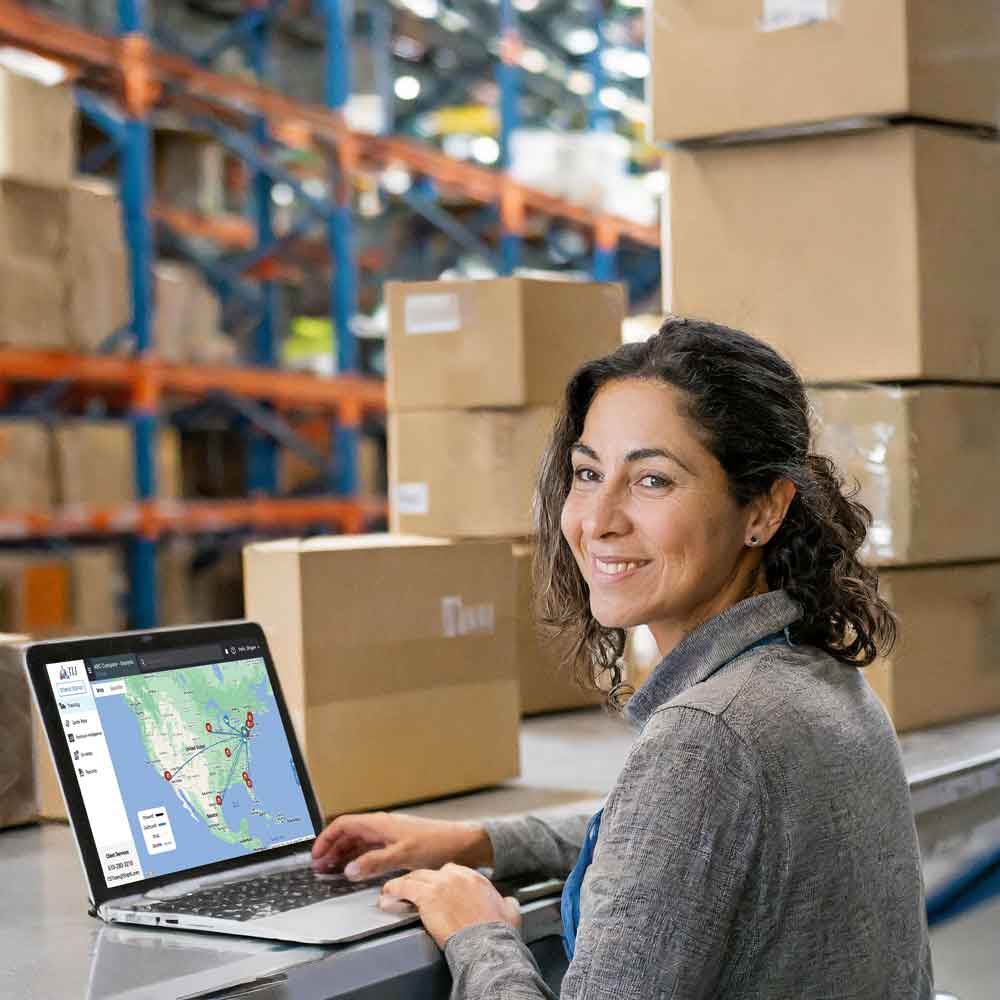
Finalizing Your Freight Classification
Shippers
calculate the density by using the shipment’s weight and comparing it to the space it takes up in storage. For instance, your shipment may be 15 lbs. per cubic foot. The lower the density, the higher the classification.
Liability pertains to the risk involved with your shipment. If you’re shipping freight containing dangerous materials, that will be clearly reflected in the shipment’s classification. If your shipment contains valuable items that increase the risk of theft, this will also play into the classification of your goods.
Monitoring classification labels on your freight invoices is critical because they can affect your final cost, and you shouldn’t have to pay for mislabeled goods. As referenced above, the more you know about freight invoice management, the more clarity you will gain on every step of the freight’s journey. Stowability refers to how easily you can stow your goods with other products, which goes hand-in-hand with liability.
These two factors are so related because hazardous materials reduce the ability to pair unrelated items nearby due to the liability involved. That said, dangerous materials aren’t the only items affected by stowability—bulky shipments that are difficult to store with other items will also affect your final fee. Speaking of bulky shipments, that leads us to the last factor, which is handling necessities.
Cargo with an irregular shape requires special handling procedures outside the standard steps, so it can impact your invoice. Fragile items also require extra care when handling to avoid breakage, which isn’t dissimilar to hazardous items. It should go without saying that dangerous chemicals and other materials require careful handling to ensure everyone remains safe during transportation. Now that you know more about the factors that affect classification, you can stop them from resulting in unnecessary charges on your invoice.
Neglecting Negotiated Discounts
Like any industry, the shipping industry often presents opportunities to discount the final price of shipments. The best way to find those discounts is simply forging a great partnership with a reliable freight shipper. However, as dependable as that shipper may be, don’t forget to double-check that they honored the discount.
Don’t worry; a missing discount doesn’t immediately mean the shipper is trying to pull one over on you—mistakes happen, but it’s your business’s responsibility to make sure your money goes where it should. Thus, neglected discounts are one of the biggest problems you can avoid with freight invoice management. It is important to also get the most competitive discounts through launching a
custom transportation RFP. An invoice may signify the completion of a shipment, but the project’s not officially over until someone looks over the invoice to ensure any previously negotiated discount gets applied correctly.
Getting Charged Twice
Another costly mistake your shipper may make is a duplicate invoice, which means you’re paying twice. Suffice it to say that this isn’t the best use of a business’s resources, especially if they don’t realize it’s happening. Thankfully, out of all the discrepancies that may occur during
freight invoice processing, duplicates are easy to catch if you’re paying close attention to all the orders going out.
Freight Bill Management
Again, this problem may make it seem like a shipper is trying to get more money from you, but it’s not always that simple. Luckily, now that you have a better understanding of the problems that can occur, you can start taking steps today to create a better invoice system. Assess your workplace today to see how you can start paying closer attention to invoices and saving yourself both money and problems.
TLI Insights
Get the latest logistics insights and tips from TLI's award-winning team. Stay ahead in transportation planning.
Questions? Email us at marketing@shiptli.com